If you’ve not heard of design thinking, then you need to check it out.
It recently even saw it features on a recent 60 minutes episode with David Kelley, the founder of IDEO. During the segment they even discuss SAP’s founder, Hasso Plattner and the human centered design work at Stanford.

SAP has fully embraced this approach to solving problems and is working with customers all over the world to help redesign business processes. I invite you to reach out to your account executive and see if SAP could do a design thinking workshop around a specific problem that your team is thinking about. The approach is fresh and new and like nothing that you’ve seen before. We can deliver activities which will help your own employees better understand their customers and creatively come up with unique insights and solutions to difficult problems.
In my experience, your end customers will often find it difficult and unintuitive to do business with you. That because we often look at what processes will make the organization more efficient and keep costs low instead of what processes will make the customer’s life easier. At its core, design thinking leverages empathy to radically change our perspective and get us thinking differently.
I have received extremely positive feedback for each of the design thinking sessions I have been involved in. People are amazed at how energized they are and how much fun it is. By the end of the day we have walls full of post-it notes, simple prototypes and storyboards.
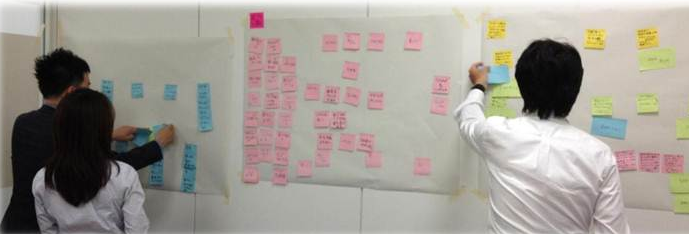
The following application is a concept application that we developed as a result of design thinking. We worked together with a diverse group of people to look at the problem of maintenance. We realized that there was a lot of information that an organization needs when repairing field assets and that not having that information can be expensive. They would need to know:
- What work orders are assigned to us?
- Where is the asset located? How long will it take to get there?
- What is the problem?
- What is the weather like?
- What tools do I need?
- How do I make the repair?
- How long will it take to repair?
- What other repairs are scheduled for this asset?
- How was this asset performing prior to the repair?
- How should this asset be operating after it’s been repaired?
We took all this feedback and put together a concept app for the iPad that encompasses all these types of questions and more.
In our case we used a wind farm scenario. Our organization has 4 wind farms that we manage. From this overview screen I am able to see the health of all my assets. I can select from multiple views including real-time views that display weather and transmission network related information.
The user can drill down into a collection of wind turbines off the coast. The alerts over the icons indicate alerts which have been raised. The color of the icons indicates the health of the asset.
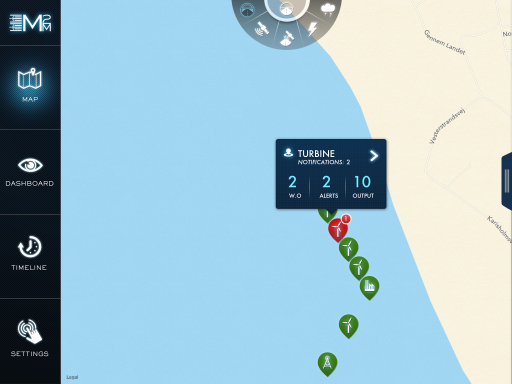
If I’m an engineer onsite, I can easily view information about an asset through an augmented reality. The ability to see information about the asset augmented on top of the iPad camera. As you pan the camera around, the information on the screen will move as well.

Once I’ve selected the asset you are able to see real-time information about how the asset is performing. I can see what maintenance has been recently performed as well as what additional maintenance is required now.
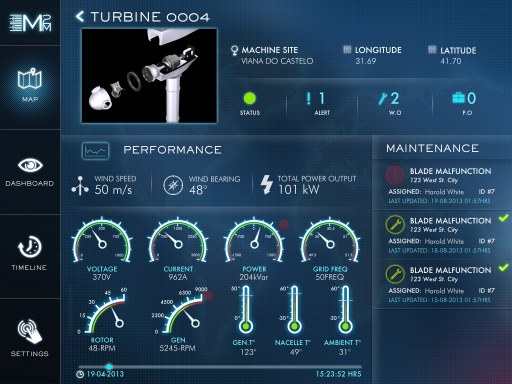
I can drill into the alert at see that although the problem was reporting as a blade malfunction, the details show that actually the maximum temperature threshold of the main coupler has been exceeded. In this case the job to repair this problem is unassigned, so I can assign it to myself.

I can see recommended steps and the output provides me future temperature outcomes based on existing predictive models.
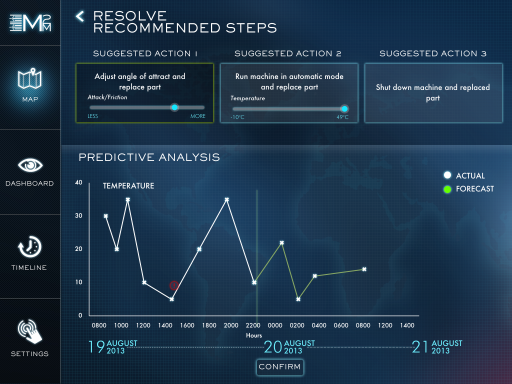
One thing that engineers would like to have is built-in instructions on how to perform a repair. Here we’ve integrated Visual Enterprise into this app so that the engineer can see step by step how to replace the main coupler.
Blade Replacement | Disassembly | Component Parts
|
---|
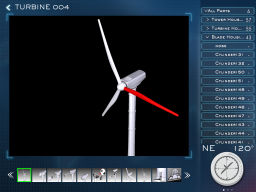 |  | 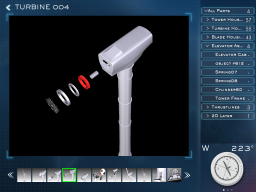 |
This view is perfect for the engineer because they can see exactly how the item is to be disassembled and reassembled.
I also have schematics just a finger tap away. When I’m up in a wind turbine I don’t want to have to walk back down because I need a schematic or need to understand more about the repair that needs to be done.

Have you considered Design Thinking?
If you have any challenges that you feel need a creative solution, SAP can help. At no cost to you, SAP will help you and your team leverage tested and proven design thinking techniques to come up with creative solutions. Through a workshop that lasts only a few hours, we’ve helped countless organizations overcome business challenges through their own imagination, inventiveness and creativity.
Contact your SAP account about scheduling a Design Thinking workshop for your team!
«Good BI»