SAP Intelligent Clinical Supply Management is an advanced solution for clinical trials to facilitate study management, demand forecasting, manufacturing, packaging, labeling, and shipments of clinical trial materials.
This blog introduces the highlights of the latest feature release 2306 of SAP Intelligent Clinical Supply Management.
Release Highlight for Study Management and Planning & Forecasting
Supply multiple treatments/dispensations from a bulk kit
During a trial, it can happen that multiple patients at a site are supposed be supplied with the same kit, e. g. that one glass vial contains several doses of vaccine which can be dispensed to different patients.
To cover these scenarios, an additional column has been added to the kit type table where information about the number of units in a bulk kit can be entered. This information becomes available also in the treatment table where you also can enter the number of units to be dispensed per individual.
Possibility of setting up placeholder site groups
When setting up a study, trial managers might not know all site groups of the study yet (site group = set of sites involved in a study that are supplied from the same distributing depot). Therefore, we have introduced the possibility to create placeholder site groups when creating a study. This enables users to start their planning without having the final lists of countries ready. As soon as the country is known, the placeholder can be replaced by the final site group.
Plan studies with switches between randomization groups
When dealing with randomized studies in SAP Intelligent Clinical Supply Management, users define at least one randomization group comprising two or more treatment groups when designing their study. Subjects then are assigned at random to the treatment groups of a randomization group according to the subject ratio described in the study protocol.
With the latest release, it is now possible to maintain relationships between randomization groups and treatment groups. This enables users to model studies with several phases (e.g., if there is a need to switch the placebo group to the active group and vice versa during a study). Of course, it is also possible to plan an additional enrolment for each phase of the study.

Figure 1: Maintain relationships between randomization groups switches directly in the Study Design tab of your Scenario Planning
Additional functionalities in demand planning: End of demand and kit type switches
To be compliant with a respective study protocol, it is now possible to hard-stop demand generation in a site group on a specific date, irrespective of potential additional planned visits. The end of demand can be directly edited in the scenario planning - for each site individually or also for all site groups at once. For a better overview, this information also becomes available in the Study Header.
In case the study protocol contains a switch from one kit type to the next after a certain duration of the study, this can now be entered directly when creating the kit types. For each kit type, users now have the possibility to define a validity date. This information is then reflected in the site events table in the scenario planning, where we have included a table for kite type switch demand:

Figure 2: Kit type switch demand can now be maintained in a dedicated table in the Scenario Planning, thus further improving the accuracy of demand planning.
With this new functionality, it is now possible to plan additional demand to supply sites ahead of scheduled kit type switches.
Genealogy report
When setting up a complex study, trial managers can quickly lose track of all the relationships between the different study entities. The new genealogy report supports this process by providing a network graph showing the relationships between a study's entities (blinding groups, kit types, label groups, site groups, materials, distributing depots) at selected validity dates. At one glance, users now can verify that everything has been assigned correctly.
More detailed demand provided for supply planning
Demand submitted to supply planning is now broken down into actual and recalculated demand based on actual enrollment, recalculated demand based on recalculated enrollment, site seeding demand, and additional demand. This detailed information is provided in the scheduling agreements where downstream supply planning tools can directly access the data and use it for a more accurate supply planning resulting in a better patient supply guarantee while at the same time avoiding costly overages.
Release Highlights for Manufacturing & Packaging
Enhanced shelf-life extension process
Shelf-life management is a special challenge in clinical trials. Besides country-specific regulations affecting shelf-life, permitted shelf-life might also change during a study due to new insights about stability and storability of the new compounds. Thus, it might be reasonable to extend the shelf-life of already produced and labeled products to save waste and production costs.
SAP Intelligent Clinical Supply Management has provided shelf-life revision process support already in the last release 2210, where shelf-life revision can be executed based on flavor IDs (reducing the proliferation of SAP materials).
In our latest release, the existing process was enhanced with some additional features:
Integration to SAP Batch Release Hub for Life Sciences
Before an investigational medicinal product can be administered to humans, it must undergo a specific batch release process. The first step is the technical/GMP release, which checks if manufacturing and testing of the batch is in accordance with defined release procedures and in compliance with Good Manufacturing Practice (GMP). An additional release step is the country/depot/regulatory release which checks for a variety of approvals by government or health authorities regarding research including human subjects. Typically, these release processes involve a lot of paperwork and require the collection of data from many different systems.
SAP Batch Release Hub for Life Sciences (BRH) replaces the paper-based batch release process with an automated and simplified batch release process.
To streamline clinical batch release processes, we have integrated SAP Intelligent Clinical Supply Management with SAP Batch Release Hub for Life Sciences, guaranteeing a seamless and smooth transfer of information from one system to the other.

Figure 4: Information flow between SAP Intelligent Clinical Supply Management and SAP Batch Release Hub for Life Sciences. Creation of an inspection lot in ICSM serves as a release trigger for the GMP release in BRH. After the usage decision has been made in BRH, the status of the inspection lot changes to “unrestricted stock”. In a later step in the process, after a Goods Receipt or Inspection Lot has been created for a specific depot, a release decision item is created for the Regulatory Country Release.
Stock Upload
For the initial migration from legacy systems to SAP Intelligent Clinical Supply Management, we have introduced a mass batch upload functionality. This functionality allows to create Packaging Control Numbers (PCNs) for existing CFG batches via mass file upload without the need to migrate process and purchase orders that have been already completed. As a prerequisite, the files to be uploaded must contain all information required to display data in the Manage PCNs app and to perform shelf-life extensions and relabeling. Before creating a PCN, the system performs several checks and raises an error if any of them fail.
Release Highlights for Distribution
Quantum picking for Inventory Managed locations
With the introduction of Quantum Picking, SAP Intelligent Clinical Supply Management supports a shipment process where the exact MedKit number to be picked can be selected directly by the warehouse worker at the time of picking warehouse task creation. This late determination of the MedKit numbers enables the warehouse worker to decide upon the selection of the respective kit based on the availability of Clinical Finished Goods in the warehouse (considering existing handling units, packaging sizes, etc.). This contrasts with the direct picking process where Medication Numbers are determined already very early in the process with the creation of the Stock Order or the Site Shipment Order and where the givens in the warehouse cannot be considered.
With the 2210 release of ICSM, Quantum Picking was already supported for SAP Extended Warehouse Management (SAP EWM) and Third-party Logistics (3PL) depots; with the 2306 release Quantum Picking is also provided for Inventory Managed locations.
Decentrally managed EWM instances in Analyze Stock at Depots app
To complete the portfolio of supported warehouse management systems, the app “Analyze Stock at Depots” has been enhanced to also support decentrally managed EWM instances.
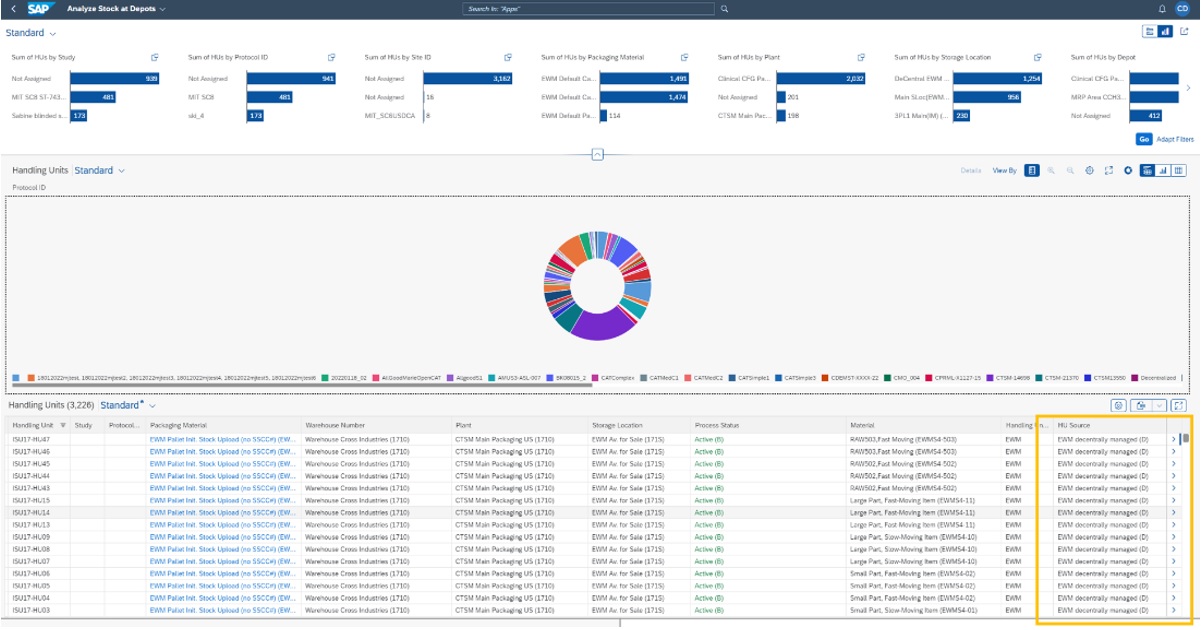
Figure 5: The Analyze Stock at Depots app also supports decentrally managed EWM instances.
With this app, users can check for Clinical Finished Goods (CFGs) and can view more details about Handling Units so that it serves as a handling unit monitor for SAP Intelligent Clinical Supply Management. With the latest release, the app supports inventory managed handling units, centrally EWM managed handling units as well as decentrally EWM managed handling units.
Manage Material Descriptions
With this new app, users can create or maintain country-specific material descriptions that are necessary for a trade compliant delivery documentation.

Figure 6: The Manage Material Descriptions app allows to maintain material descriptions necessary for a trade compliant delivery documentation.
The material description text is then made available for printing in the import advice document or for purchase order printouts.
ICSM-specific enhancements of several apps
Monitor Purchase Order Items app
To provide users with a faster time to information about all purchase-related processes that occur during a clinical trial, we have enhanced the SAP S/4HANA app “Monitor Purchase Order Items” with several field specific for clinical trials (Study, Protocol ID, PCN ID). Wherever possible, we have also included hyperlinks to other applications so that it can serve as a central entry point to access all purchase-related documents.

Figure 7: The Monitor Purchase Order Items app provides users with a faster time to information about all purchase-related processes.
PCN fields in various additional apps
For most customers, PCN is the central parameter in clinical trials. We have therefore enriched several apps in ICSM with information about PCNs such as PCN ID, PCN Status, PCN Expiry Dates. With this information, users can achieve an increased transparency of blinded batch information for logistical follow-on processes.
List of enriched apps:
- Material Document (Overview)
- Manage Sales Orders
- Manage Inbound Deliveries
- Manage Outbound Deliveries
- Manage Purchase Orders
- Assign Batches to Purchase Order Items
What is left to say?
The features that have been illustrated in this blog do only represent some of the highlights of the release. For more information about the latest features of SAP Intelligent Clinical Supply Management please check out the
Help Portal with its
What’s New Pages.
To make sure you don’t miss the next New Features articles, we would like to invite you to follow the tag
SAP Intelligent Clinical Supply Management”. We are also happy to receive your feedback,
questions or thoughts in a comment.